Respect for People in the Production System
What are we missing in the OpEx movement? We have talked so much about the Six Sigma and lean thinking, and how the two, used together (not just one or the other) lead us to operational excellence. Is respect for people the missing link?
When I went to Kentucky, two decades ago, to study Lean Manufacturing with other members of the Bluegrass Automotive Manufacturers Association (BAMA), what impressed me most was that we were taught “respect for people.”
A few months ago, I joined a book club which met weekly (online), to discuss “Learning to LEAD, Leading to LEARN – Lessons from Toyota leader Isao Yoshino.” Reading the book (written by Katie Anderson) and participating in the weekly discussions, I got reminded that Toyota’s people-centered culture (“We make people like we make cars”), along with a strong commitment to continuous improvement, are foundations upon which their production system was built upon.
Now, hearing or reading this, “respect for people” or “respect to people,” knowing it is not equal to doing it. Our purpose is to be doers, respectful of our team members, and reap the benefits of a world-class production system, ever ready to meet challenges that may come.
Not Toyota Disciples
I wish to point out that I am not a die-hard Toyota disciple, not do I believe the good manufacturing practice I write about—Respect for People– is their invention. Truth is, this is embodied in many of the world’s articles of faith, both amongst the religious, non-religious and even the atheists.
Let’s look at the United Nations Global Compact, taking note especially of the first two principles: human rights.
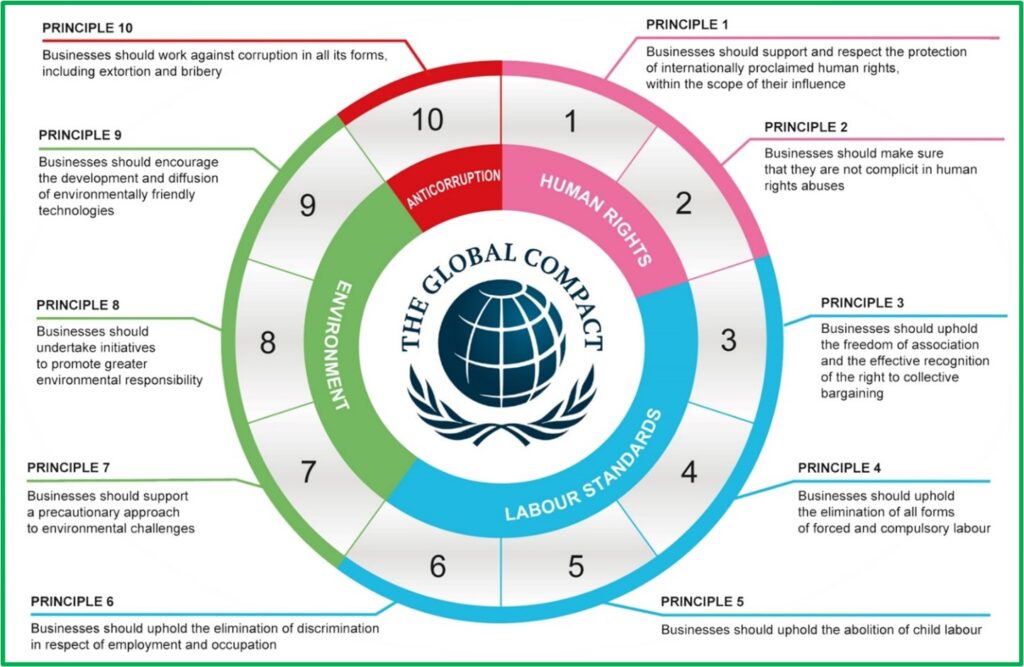
The difference is how this Respect for People is literally lived as way of life, with Toyota as a leading example. It’s not just knowing or believing–it’s acting on the belief—actions! Not lip service.
A Lesson from Kentucky
Obviously, if we aren’t vigilant, we can be respectful and doing things right for a long time, and suddenly, we may “miss the mark.” In the plant where the BAMA training was held, we were told that a plant manager was let go, “because he didn’t respect a team member.” The rule iwa that everybody deserved respect, regardless of rank in the organization.
If everybody in the team felt respected and valued, the easier it was for them to give their best and fully support the organization. As a demonstration of that respect, during our plant walk, our trainers pointed to us the shelves of supplies (gloves, markers, pens, etc.) by the aisle from the employee entrance going to the production floor. That showed that they trusted they team members to take only what they needed at work; they wouldn’t take anything extra to bring home. “If we can’t trust them, why did we hire them?” So said our chief training instructor.
This is not an example of what every plant or workplace should do. But it shows what can be done at some point. Companies just starting out would be at a different level than those who started out well ahead, and are getting closer (at their own pace) to what we saw as a model of trust and respect. Our trainers indicated they weren’t afraid to show us what they have already achieved in their plant, even if some of us came from competitor companies.
Because it took them a lot of time to reach their current level (at that time). They expressed confidence that if we copied them, it would take us a long time too, and “by the time you reach our current level, we have moved to higher levels already, you can’t catch up with us.”
Even Toyota itself isn’t worried about the competition learning the Toyota Production System. Jeffrey Liker, who studied Toyota for 35 years, in the second edition (published just months ago) of his book The Toyota Way, writes that the company created the Toyota Production System Support Center to teach US companies. It has been spun off as a non-profit and does free work for other non-profits and charitable organizations and paid work for private companies.
Commitment to Continuous Improvement
This is the other side of the coin. Both in the training handouts given at Kentucky, and the book written by Katie, a lot is about team members contributing to the CI efforts.
Can an organization continuously improve, reach new heights of efficiency, productivity, and quality just with “The Toyota Way,” or the Toyota Production System (TPS) apart from the Six Sigma methodology. I suggest yes! (Note: Lean manufacturing was not a term originally used by Toyota to describe their system. Lean was coined by the west, and many companies implementing lean customarily describe theirs as X Production System (replace X with one’s own company name).
There was a time when the experts had to choose between lean or the Six Sigma methodology. Later, it was realized that they weren’t exclusive of each other, but rather are complementary tools to achieve operational excellence.
In fact, I might say that it is disrespectful for a Six Sigma enthusiast to assert that those who aren’t very good in statistical tools, can’t accomplish much CI. One Six Sigma consultant and implementation I know, suggested you have to score 100% in all the quizzes for the Statistical software he recommends, to be able to do a good job and be certified with a belt. With this high bar, we will disqualify many members of the CI Team, when what we want is for everybody to be involved in the Continuous Improvement efforts.
What Matters is Doing, Not Knowing
To achieve operational excellence, we need to practice, apply our knowledge. And avoid mistakes committed by others. Many times, experience is not the best teacher; it can be an expensive teacher, if we don’t learn from and avoid repeating the mistakes of others.
I particularly liked the recommendation of one author-consultant I have worked with, as follows: Each manufacturing location (or a service organization) needs a full-time Black Belt (100% of his time spent on three to four major CI projects a year). This BB must be supported by anywhere from three to five Green Belts (who can help, up to 50%o their time, on one CI project a year).
As CI projects aren’t done in a vacuum but with a multi-disciplinary team, the organization needs as many as possible of their staff to be trained on the CI methodology, at the Yellow Belt level. (At the location of my Lean training, their job applicants wouldn’t even be called for an interview (at that time), if they haven’t completed Phase 1 of their lean training. That training was provided to interested applicants who, if they got jobs elsewhere our trainer said his company didn’t mind, it’s their company’s contribution to the community.)
Effective Leadership is Key
Training and willingness of our people to help advance the CI initiative won’t do much, without the leadership’s support.
That support cannot be passive; should be persuasive and effective. Well, everybody knows this, so what’s the issue? To answer this question, we’ll take a look at an actual case study.
The new chief operating officer (COO) of a company brought in an external consultant/CI implementation partner, to train at least one Black Belt from each of the group’s member companies (manufacturing plants). The trainees (some of them flown in from different parts of the world) had to sign a letter of undertaking that they wouldn’t leave the organization for a specified period of time. It’s natural for the employer to want to reap the benefits in-class trainings and mentoring by the consultant.
The general managers of the various divisions and manufacturing locations were also called to headquarters, and given an orientation as CI Champions – to clear the path and remove obstacles, provide resources and assistance to the Black Belts in completing CI projects. The COO authorized the hiring of replacements who would take the old (non-CI) assignments of the Black Belts. The corporate office also provided the BBs with the same tool used by Plant Controllers, to calculate the CI Savings achieved on their projects; the BB’s calculations would be subject to the Controllers’ verification and attestation, before the figures ($ savings) are accepted into the “Global CI Savings Tracker” data base.
It appeared that many plants did allow their Black Belts to work full-time in CI. On a few, there were varying degrees of non-compliance.
The Worst of the Worst – A perfect example of “What We Wouldn’t Want to See”
Firstly, the BB in this particular location wasn’t freed up of his old workloads (which were already more than a full load). The plant management decided the BB projects would be just additional and concurrent activities.
The external consultant and the consultant’s counterpart at corporate were both unhappy with the slow progress at the plant, and kept asking the BB-trained CI person when he would work full-time and be reporting his Cis for tracking. The BB informed the consultant, and the COO, that he would do so as soon as he’s freed up of his old functions. But instead, the plant gave more of the same old work, non-CI projects like “new business launch” and production ramp up.
The BB was required to work weekends, to which he agreed to work Sundays but not Saturdays his religious day off, like an orthodox Jew (never a problem, not an issue the previous years). The BB was told he could not ask for religious accommodation, not anymore; the time to ask was during the job interview and prior to signing the employment contract. Plant management indicated they were at liberty to change the work conditions anytime, from 40 hours a week (Monday to Friday) to include weekends when required.
The BB did not agree, and asked for transfer back to corporate where he worked prior to the plant assignment. Head office human resources manager indicated she had to ask the plant how soon employee could be released by the plant, for transfer back to corporate.
The employee was fired, instead of the plant management agreeing to or endorsing the transfer. The terminated employee went to the human rights tribunal, asked the company’s chief executive officer (CEO) to not provide a lawyer to defend the plant human resources manager, the plant general manager (they jointly did the termination) and the COO who did not intervene to stop or negate the firing.
In the end, the long and short of the story: The COO, general manager, and plant HR manager are no longer with the company – no announcement why, unknown if any relation to the BB’s firing. The employee was offered a settlement package, but no admission from the company of any wrongdoing with respect the alleged human rights violation (freedom of religion).
I am very much aware of the facts regarding the above incident. I was wondering why, after the very promising start of the recent COO’s company-wide, multiple-plants CI initiative, this happened. A new COO was hired. (I have seen a similar thing, minus a human rights case, happen in a non-manufacturing setting – in the white-collar service industry, during the era of Business Process Reengineering, BPR.)
And then, during one of the book club’s weekly sessions, we came to discuss Toyota leader Isao Yoshino’s two-year “bad boss experience.” Four pages (Lesson #6) of the 310-page plus “Learning to LEAD, Leading to LEARN” was titled “Learn What Not to Be as a Leader,” sub-heading “Even Toyota Has Some Bad Leaders” — practicing the opposite of people-centered leadership. (Note: The book’s author Katie Anderson and the subject of her book, Yoshino, both joined our book club’s final Zoom meeting and we learned some additional information not covered in the volume. As well John Shook –the first American hired by Toyota and given a boot-camp training at Japan—joined our book club’s final session.)
We Can Do Better!
I suggest that all of Six Sigma statistical tools and/or knowledge of lean can, and will, still lead to failure and very sad human experience, if missing in the equation is “Respect for People.”
Let’s end this article with the United Nations Global Compact, taking note especially of the first two principles: human rights. But wherever we are in the spectrum, it’s never too late to start doing better. Because we can!
About the Author
Vir Alvaran is a continuous improvement professional, with over three decades of CI experience under his belt, in the Asia-Pacific and North America. He is a recipient of the Citicorp/Diners Club International Franchise Network Service Quality Award and served as president of the Philippine Institute of Industrial Engineers. He worked for twenty years in automotive parts manufacturing engineering, supplying components and sub-assemblies to the OEMs in North America.
Vir now owns a consultancy, “Closer to Lean” based in Toronto, Canada where he helps companies improve their operational capabilities.