Operational Excellence & Challenges Faced in a CO2 Removal System
In 2010, Engro Fertilizers commissioned the world’s largest single-train ammonia-urea complex capable of producing 3835 tpd prilled urea. This Plant is equipped with aMDEA Based CO2 Removal System to make the process more clean and energy efficient. This paper presents operating experience of BASF aMDEA in a CO2 removal system of this new Ammonia Plant. It also shares the problems encountered during pre-commissioning, commissioning and normal operation phase with aMDEA system.
Synopsis
Engro Fertilizers Limited operates two ammonia plants. Both plants have design capacity of 1550 MTPD and 2190 MTPD respectively and they use natural gas as feedstock and fuel.
The first plant was designed and constructed by Bechtel. It was commissioned in 1991 and it uses a hot potassium carbonate system (Catacarb) for CO2 removal. However the second plant was designed and constructed by Topsoe & SAIPEM and was commissioned in 2010. Due to the difference in age and energy costs at the time of design; specific energy consumption of the new plant is much lower than the first plant. Main contributing factors to lower specific energy consumption are lower steam/carbon ratio, high front end pressure, high steam pressure, better heat recovery in convection zone and BASF aMDEA system.
Introduction
Engro Fertilizers Limited is the second largest Urea manufacturer in Pakistan. Engro formerly Exxon Chemical Pakistan Ltd was the most successful employee buy-out in Pakistan corporate history. Engro manufacturing site is sited in a small town of Pakistan, rich in gas resources, known as Daharki which is some 600 km north of the famous Port City of Karachi.
The original ammonia-urea plant, with self-sustaining utilities, was commissioned in December 1968. The capacity was 173,000 (MeT) of Prilled Urea per annum. This was 80% of urea market share in the country at that time. Over the next 22 years, the plant was debottlenecked in several low cost steps to enhance a production capacity to 270,000 MeT of Urea per annum.
In 1991, Urea production increased from an annual capacity of 270,000 MeT to 600,000 MeT after the inauguration of relocated ammonia and urea plants from Pascagoula (USA) and Bellingham (UK) respectively. It further increased to almost 1 million tons in 2006 after a series of revamps and energy conservation projects.
In 2007, based on increasing Urea demand within the country, Engro took initiative to put a new Ammonia-Urea complex for meeting those requirements. The project was initiated in 1Q 2007 & production started in Dec 2010.
After the commissioning of the new plants in 2010, annual capacity of the site has increased further to 2.3 million tons of urea. Engro has accomplished significant progress not only in its base urea fertilizer business but also in other diversified projects. Other businesses include;
- Engro Foods
- Engro Power Generation
- Aventac Automation
- Engro Polymer
- Engro Eximp (Rice Business)
- Engro Vopak Jetty Business
These businesses along with fertilizers are being operated by independent companies under the umbrella of Engro Corporation.
CO2 REMOVAL SYSTEMS AT ENGRO
Hot Potassium Carbonate Process
Hot potassium carbonate solvents (K2CO3) are used with appropriate activators (DEA or glycine) and corrosion inhibitors (V2O5 and As2O3) in Benfield, Carsol and Vetrocoke processes.
Process | Solvent | Activator | Corrosion Inhibitor |
Benfield | K2CO3 | DEA | V2O5 |
Carsol | K2CO3 | DEA | V2O5 |
Original Giamarco Vetrocoke | K2CO3 | Glycine | As2O3 |
New Vetrocoke | K2CO3 | Glycine | As2O3 |
Corrosion: K2CO3 reacts with CO2 to generate the very corrosive KHCO4. Corrosion inhibitors such as vanadium oxide V2O5, arsenic oxide As2O3 or potassium dichromate K2Cr2O7 must therefore be added in large quantity. For instance quantity of arsenic comprises 10–15% of the total volume of solvent being circulated.
Toxicity: The corrosion inhibitors are indeed very toxic and are listed as poisons in all the industrial countries. Hence disposal after usage is an important concern for all the plants handling these chemicals nowadays & EPA regulations are getting tougher day-by-day
Activator Make-up: All the corrosion inhibitors oxidize DEA or glycine activators. Therefore these activators must therefore be made up continuously in the system
Waste of Energy: In order to allow an effective absorption of CO2 and a limited loss of solvent the temperature of lean and semi lean solvent fed to CO2 absorber must be low. Therefore lean and semi-lean solvents are therefore cooled down by water in heat exchangers before they are fed to the absorber. Consequences are loss of energy and consumption of cooling water
aMDEA Process
Toxicity: aMDEA is a biodegradable and non-toxic solvent (harmful for human body as any amine but not declared as a poison).
Corrosion: aMDEA is much less corrosive than the other amines or Potassium Carbonate. It does not require any toxic corrosion inhibitors and it even allows, in some particular cases, the use of carbon steel for some parts of equipment.
Stability: aMDEA is a highly stable solvent that does not decompose, foaming tendency is therefore reduced. It cancels the need of a reclaimer unit. Hence, monitoring and analysis requirements are minimized.
Make up rate: The blow-down stream is minor and is only aimed to avoid any buildup of catalyst dust of HTSC and LTSC shift conversion by-products. Losses are mainly mechanical losses such as pump switches or pipe drainage. Vapor losses are minor. Consequently, make up rate is less and can be evaluated in the range of 3 – 10% of the initial fill per year.
High performances: In addition to these trouble free operation features, aMDEA solvent also bring consistent and measurable economic benefits:
- Very low CO2 content in the treated gas
- High CO2 purity and recovery (inert gases co-absorption is minimized)
- Low energy consumption
aMDEA low CO2 content in the treated gas:
The comparison of CO2 content is given below for Carsol, MEA and aMDEA technologies
CO2 content min, ppm | CO2 content max, ppm | |
Carsol | 800 | 1200 |
MEA | 50 | 100 |
aMDEA | – | 100 |
Overall aMDEA Compared to Hot Potassium Carbonate System
- Non corrosive solvent
- No toxic corrosion inhibitor required
- No passivation required
- Significantly lower thermal energy consumption
- No solid precipitation in the solution
- No special heat tracing requirement
- No environmental problems
- Minimum analytical requirements
- Easy to operate, very “forgiving” and robust process
The Journey of aMDEA Operation @ Engro
Pre-Commissioning of aMDEA System
After adequately furnishing themselves with every tool in their munitions, Engro’s operation team exhibited a splendid display of their skills in the field. The journey which started from P&ID systemization, manpower buildup, training, SOPs development, pre- commissioning, commissioning and startup came to a successful end.
aMDEA system was relatively new to Engro, and the team which was gathered to operate this unit was also not well experienced on aMDEA operation. So the challenge was to streamline system without any upset. For this a lot of brain storming was done to see worldwide practices and a detailed plan was chalked out to build up through understanding about the system through trainings and to follow the best practices in pre-commissioning phase for having system smooth run later on. Main concerns were pumps abnormal behavior and foaming in the system due to Foreign materials / grease.
aMDEA Section Commissioning major milestones are summarized on the right.
The journey from pre-commissioning to commissioning went through following steps based on extensive brainstorming sessions etc.
1. Pre-Cleaning of Tower’s Packing (external washing)
During brainstorming, it was thought thru to avoid excessive contamination & foaming in system by washing all packing prior to loading in towers.
Column’s packing was washed with soap solution to remove grease, dust and foreign material and then dried with air. It helped a lot in smooth and reliable commissioning of aMDEA system.
2. Water Flushing, Purge and Tightness Test of all Vessels
Another step we took for system reliable commissioning was to flush towers, vessels and heat exchangers with water after loading of packed beds and installation of redistributors. This was done to remove grease or coarse grime that might have been introduced during construction / shipment.
As a part of contingency planning, columns were purged and pressurized with nitrogen for tightness test so that any leakages could be addressed prior to the introduction of natural gas. This helped in attaining ZERO leakage during commissioning
3. Flushing with Potassium Solution
In second step of Pre-commissioning, aMDEA system was flushed with hot potassium solution (~ 3% w/w) for a period of 12 hrs. The temperature of the solution was maintained at 50 – 70 ºC to ensure proper removal of any coating material.
Side-stream filtration circuit also remained in operation to remove any coarse grime or grease which might have been left during initial flushing process.
Before start of this circulation, all aMDEA pumps suction strainers were reinforced with sacrificial meshes (50 microns) to remove foreign particles. Pump’s suction strainer choked immediately after the start of the circulation. Insulation material, plastic, debris was removed during the course of potassium solution circulation. (see Fig 3)
4. 1st Flushing with Demineralized Water
After completion of hot Potassium Flushing, aMDEA system was then flushed with hot DMW (~ 70 C) to remove traces of potassium solution and left over coarse grime or foreign material. Circulation duration was 10 hrs. to ensure water circulation through all parts of the system.
Solution pH (< 9) and foaming tendency (foam volume < 300 ml, collapse time < 20 sec) was checked after the completion of hot DMW circulation to gauge the adequacy of this circulation. System was then completely drained to sewer.
The circulated water had a reddish brown color and foam test indicated formation of very stable foam (collapse time greater than 5 minutes). After filtering the system, the foam activity was reduced to normal values.
5. 2nd Flushing with Demineralized Water
aMDEA system was then again flushed with hot DMW to improve system conditions and achieve desired results. 2nd flushing with DMW was carried out for a period of 10 hrs. at a temperature of ~ 70 C. Later complete system was drained. At this step complete draining was ensured through a number of locations to avoid any water inside before adding of AMDEA to the system.
6. Preparation of aMDEA Solution
The final milestone in Pre-Commissioning was to charge aMDEA in the system. aMDEA solution (with 50 % w/w concentration) was fed to the system to account for any dilution after circulation establishment due to water accumulation in the packed beds.
The solution circulation was continued for a period of 10 – 15 hrs. to reach working solution strength of 40 % (w/w) amine concentration with an addition of 40 kg antifoam in aMDEA section to control foaming.
COMMISSIONING / OPERATING EXPERIENCE
As the uphill task of the plant’s commissioning was Engro’s responsibility, the target was to stream line all the sections including aMDEA in the first attempt. Team experience was lean so all the operational team went through extensive class room trainings to familiarize with the new process. The general impression was that the operation of the CO2 removal system would not be much different. In essence this was true. However, we experienced that the advanced BASF aMDEA system had some specific properties that put operators again on the learning curve to get acquainted with the system.
Overall aMDEA system has been fairly steady except for the need to dose slightly more antifoam than was originally anticipated. Overall there are more benefits than originally envisaged, such as reduced solvent circulation rates, lower regeneration heat load & reduced heat rejection to cooling towers.
Operators were confronted with the following major upsets:
- Foaming in LP flash vessel (V-301) and Absorber (C-302)
- Abnormal behavior of aMDEA high and low level switches
- aMDEA solution carry over from LP Flash Vessel (V-301)
Apart from these operational issues, the following additional problems were experienced:
- aMDEA losses were far greater than anticipated
- Amine smell
- Vibration Problems in Lines and pumps
Extensive efforts were made to understand the nature of these upsets. By monitoring the end results, a better understanding was created and experience was gained to manage safe operation. The following briefly describes the journey;
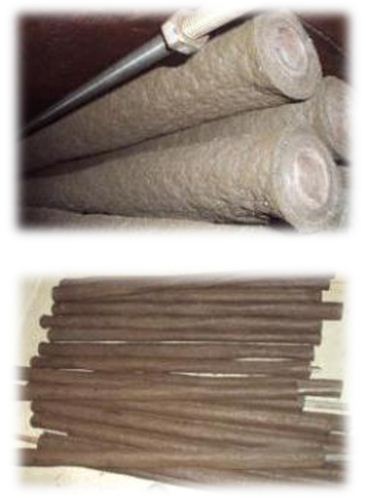
1. Antifoam Dosing
Antifoam dosing had been quite problematic since the commissioning of the plant. Amerel-1500 was being mixed with water in a proportion of 0.5 L (antifoam) to 125 L (water) but it had been observed that the dissolution of Amerel-1500 wasn’t very good, due to which it settled down at the bottom. Due to this issue the LG of the antifoam tank also remained erratic, and it was very hard to get an idea that how much antifoam had actually been dosed at any point of time.
Due to lack of system knowledge, antifoam dosing rate was quite high at the start resulting in frequent choking of side stream filters. The side stream filters were first commissioned with 10 microns polypropylene cartridge filters & then switched to 5 microns filters.
Following antifoam dosing strategies were devised based on experience and system behavior
- Initially antifoam was being dosed directly to LP Flash vessel
- Antifoam dosing strategy was then changed to parallel dosing in all columns
- Now a day’s antifoam is being dosed in series to all columns (6 hrs. in LP flash vessel, 2 hrs. in Absorber and 1 hrs. in HP flash vessel) & is proving effective I controlling system variation well in range.
To avoid antifoam settling, steam coil is provided in antifoam tank to have better mixing of antifoam in hot water. This modification will not only improve system performance but will also reduce risk of sudden dosing of antifoam slugs due to improper mixing
Antifoam dosing strategy has gone through the trial and testing phase and is now vouching for the effectiveness of the system.
2. Foaming in the Columns
During the first month of operation, foaming was a major problem. Foaming was detected by changes in column levels and pressure drop across the columns.
By adjusting the amount of anti-foam agent and by switching to continuous dosing the foaming problem was brought back to an acceptable level. We learnt that too much anti-foam agent can also cause foaming. Also the deterioration products of the anti-foam agent could cause foaming.
During initial stages of the plant operation anti-foam dosing rate was not known, with experience and continuous operation we learned the optimum dosing rate and strategy of anti-foam agent (hit and trial method).
3. aMDEA Towers High and Low Level Switches Abnormal Behavior
Wrong actuation of low and high level switches of aMDEA towers; (stripper, absorber and flash vessel) was observed numerous times and resulted in the tripping of circulation even though the level remained in normal range. This abnormal behavior was due to foaming and accumulation of antifoam in the dead legs of switches. Security trips were then moved to level transmitters to make system more reliable.
In order to avoid any nuisance tripping (due to transmitter malfunction) and make this system foolproof a modification was made later for installation of second new transmitters on all columns. This switches issue is still under study by SAIPEM & they are evaluating the proper solution.
4. Amine Smell
Immediately after startup, we were confronted with a very strong amine smell in CO2 stream.
The smell was caused by the presence of amines, especially trimethylamine (TMA) in the CO2. Amines are produced across the LTS catalyst by the reaction of ammonia and methanol. Trace levels of NH3 are produced across the reforming and HTS catalyst and methanol is formed as by-product over the LTS catalyst. The higher the methanol concentration, the higher the amines concentration in the LTS effluent.
The methanol concentration was high after the initial startup for two reasons;
- LTS catalyst was new.
- Steam/Carbon ratio at the inlet of the primary reformer was high which had been decreased over the period of time. Steam to secondary reformer had also been decreased from 20 tph to 5 tph. This resulted in decline of the steam/dry gas ratio at the inlet of the LTS from 0.63 to 0.4. This had a great impact on the methanol formation.
Over the period, methanol production across LTS decreased as the catalyst aged and consequently the amine formation decreased.
5. Vibration Problems in Piping & Pumps
Soon after the circulation establishment, too much vibration was observed in the lean and semi-lean solution piping (just after lean solution pump discharge and LP flash vessel inlet)
Design calculations were checked and it became clear that solution inlet velocity was too high, resulting in the piping vibrations. The following measures were taken to minimize the impact of excessive vibration and prevent recurrence:
- Semi lean solution from HP flash vessel to LP flash vessel supports were strengthened
- Additional supports provided on lean solution pump discharge piping in consultation with SP
- Solution letdown from HP flash vessel to LP flash vessel through LV-3014 A/B, control shifted from split range to parallel which helped a lot in reducing line vibrations
The measures taken have proven to be successful since no other major piping vibration issue occurred.
Lean pump operation remained problematic due to high vibrations. A lot of troubleshooting and flow dynamic analysis were done by SAIPEM Machinery experts and ENGRO team to address the issue. Later it revealed that one of the major causes was through priming of the pumps before putting them in operation as gas bubbles in solution led to in efficient pump operation and hence high vibrations. By changing the practices for solution filling and system purging before startup, this issue got under significant control.
6. Recycle Gas Compressor (K-301) Problematic Operation
The flash gases from HP flash vessel are routed to K-301 (recycle gas compressor) from where the compressed gases are recycled to CO2 absorber for recovery of hydrogen and CO2. Since commissioning, recycle gas compressor remained problematic. Due to high inter-stage parameters (pressure and temperatures) resulting in the failure of inter-stage valves and loss of ammonia production due to frequent equipment breakdown for maintenance.
K-301 inter-stage valves were replaced and inspected numerous times against passing but no appropriate root cause identified. Machine is still under observation in correspondence with Vendor for root cause analysis.
FLOODING INCIDENT
Flooding in LP Flash Drum, V-301
On April 2nd, 2011 @ 1621 hours, sudden fluctuations in level of LP Flash Drum occurred followed by rapid level increase in overhead separator, V-303 and downstream K.O drum, V-19. Finally high level in V-19, CO2 Compressor suction KO Vessel tripped CO2 compressor and I-4 (trip of aMDEA circulation pump) was manually activated at 1636 hrs. i.e. 15 min and 30 sec after the fluctuation commenced. Significant amount of aMDEA discharged through the CO2 vent downstream of overhead separator, V-303 during the incident. Sequences of events that pursued are mentioned below.
Time | SOE |
1625 hrs. | Decrease in CO2 pressure from 0.51 to 0.32 kg/cm2 |
1625 hrs. | Sharp decrease in the level of LP Flash Drum, V-301 from 41.7 % to 10.4 % in 4.0 min |
1626 hrs. | Anti-surge valve of CO2 compressor was immediately opened to increase CO2 pressure which got increased and resulted in opening of CO2 vent (PV-3015 A/B) |
1626 hrs. | aMDEA solution showering from CO2 vent, PV-3015 A/B was observed |
1629 hrs. | V-301 low level security bypassed in view of wrong level indication |
1629 hrs. | V-301 low level security bypassed in view of wrong level indication |
1630 hrs. | Increase in V-301 overhead K.O Drum, V-303 level from 51 % to 100 % in 1.0 min |
1630 hrs. | Solution shifted from V-302 (HP Flash Drum) to V-301 (LP Flash Drum) to increase its level |
1631 hrs. | V-301 (LP Flash Drum) level restored but started to decrease again |
1634 hrs. | Level increase in CO2 K.O Drum, V-19 was observed |
1635 hrs. | CO2 compressor tripped on high level of K.O Drum, V-19 |
1638 hrs. | I-4 (trip of aMDEA circulation) manually actuated when level of V-301 reduced to ~ 5% |
Incident was examined by review of the historical DCS data where following changes in key parameters were noticed;
- Severe fluctuations in V-301, LP Flash vessels level in short period of time.
- Pressure drop across the packed bed increased by 0.17 kg/cm2 – from 0.19 kg/cm2 to 0.36 kg/cm2 – during the first flooding (level decrease).
- Pressure drop across the packed bed increased by 0.18 kg/cm2 – from 0.24 kg/cm2 to 0.42 kg/cm2 – during the second flooding (level decrease)
- V-303, LP Flash Drum overhead separator level increased with 30 sec from 50 % to 100 %. 1.4 min after the level in V-301 started to decrease
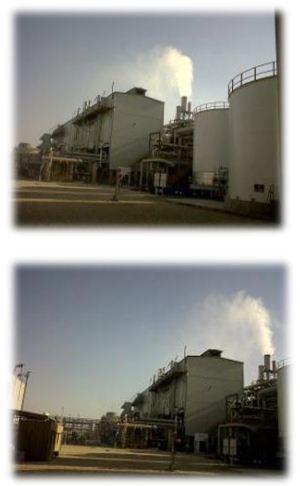
The level decrease rate in V-301 corresponded to the liquid flow rate in the column, which revealed that complete flooding had occurred in the packed bed. Flooding occurred two times, because the first flooding resulted in liquid carry-over to the column overhead line. This increased the upstream pressure due to two phase flow in the line and thereby reduced the gas/vapor flow through the bed. The lower gas/vapor load diminished the flooding and the hold-up liquid was released from the bed.
The subsequent decrease in the pressure after the liquid ceased in the overhead line re-established the high gas/vapor flow through the packed bed and triggered the second flooding. In addition, rich solution flow from C-302 (absorber) via V-302 (HP Flash Drum) to V-301 (LP Flash Drum) was increased to alleviate the level decrease in V-301, which probably aggravated the foaming / flooding problem.
The flooding occurred presumably because of the sudden and excessive foaming in V-301. The relatively high re-boiler duty owing to high S/C ratio and lower boiling point of aMDEA (due to low pressure and low solvent strength) in the re-boiler may have contributed to the rapid development from foaming to flooding. Another reason was that the side stream filtration system was not being kept in service continuously.
Scrutiny of the historical DCS data didn’t reveal any warning of foaming and the foam test results of the solution were also within the normal range. However, if the foaming was triggered by a sudden release of sediments in the bottom vortex breaker of C-302/V-302, it might have occurred instantaneously and without being revealed in the foam test of the solution.
Learning’s from the Incident
Following operational guidelines were recommended after the foaming / flooding incident in V-301 (LP Flash Vessel)
- Side stream filtration shall be continuous with a flow rate of 50 – 60 m3/h
- Level changed resulting in increased flow rates to the columns must be carried-out very slowly
- Dosing of antifoam shall be limited to 1000 ml/day unless the system indicates increased foaming tendency
- Pressure in V-301 shall be maintained at 0.65 – 0.75 kg/cm2.g
- Minimum solvent strength to be maintained at all times @ 38%. A lower solvent strength will lead to lower CO2 capacity and risk of corrosion.
MODIFICATIONS
Following points have been pondered over to ensure safety and integrity of the unit in conjunction with the optimization of the operating parameters;
1. Loading of aMDEA Solution
During fresh loading of aMDEA solution into the solution makeup tank, it was observed that it has natural tendency of having more suspended particles due to open area around dosing nozzle which cause foaming in the system despite of keeping side stream filtration system in service.
Fine mesh was installed at solution preparation tank (T-302) inlet to avoid ingress of such particles during fresh solution loading
2. Antifoam Dosing Injection Point Modification
Initially antifoam was being dosed at RP-301 A/B outlet line (rich solution) and P-302 A (lean solution pump) suction line. In case of RP-301 A/B or P-302A shutdown antifoam dosing couldn’t be carried out properly. To address this issue, antifoam dosing line was re-routed from RP-301 A/B individual outlets to common outlet line of RP-301 A/B and LV-3026 C/D and common suction line of P-302 A/B.
3. aMDEA Drainage System
Original aMDEA drainage system was slightly different from what SAIPEM provided at FFC-2 and other plants. At Engro all pumps suction drain lines, priming bleeders, side stream filtration system drains were originally collected in SY pits nearby and come to concrete pit. Floor washings and other dirty water drains were also routed in the concrete pit, posing difficulties in recovering costly aMDEA solution from large amount of dirty water.
As a part of KAIZEN (to enhance clean aMDEA solution recovery back to the system), pumps’ suction drain lines, priming bleeders (lean, semi lean and split stream pumps) and side stream filtration system drain lines were routed to aMDEA solution preparation tank (T-302) which therefore allowed small quantities of costly aMDEA to be recovered into the system.
4. Nitrogen Line to C-301 (stripper) for Pressurization
During initial startups, it was observed that prior to gas line up to aMDEA section, C01 / V-301 pressure control became very difficult due to low pressure and subsequently low suction head. To improve system operation in that part of startup, a Nitrogen connection was provided at C-301 for pressurization purpose and to give proper suction head to lean solution pumps (P-302 A/B). This has made system operation more smooth and trouble free.
5. Priming Bleeders at E-304 (DMW Pre-heater)
Two 1 ½” priming bleeders were provided at E-304 shell side and routed to solution preparation tank (T-302) in order to remove trapped air from the circuit during lean solution line filling for pump startup. It not only helped in reduction of line vibration but also reduced pump’s cavitation.
6. Seal Flush Line to P-303 A/B (Split Stream Pump)
As per original design, polish water was provided for P-303 A/B seals cooling which not only disturbed system water balance but also reduced solution concentration over the period of time.
In order to resolve this issue, new seal flush header was provided from lean solution pump’s discharge (P-302 A/B) to seal flushing header to P-303 A/B seals in addition to PW connection. This modification helped in managing water balance.
SUMMARY
The commissioning & stabilization of aMDEA unit has been a roaring success. With concerted efforts, excellent planning and preparations, the new CO2 removal system’s commissioning was not only accomplished well within the scheduled time but also in-house optimization efforts proved successful in realizing its excellent performance. The decision to rely on in house operational capabilities while identifying the leading limiting areas and their subsequent step-wise improvement paid heavy dividends.
No doubt, some problems were faced during the course of the project and the team got stuck at some points, but they got thru with continuous zeal and efforts. Still aMDEA operations have some unrevealed areas and the team is putting effort into getting a hold on them for achieving excellence in the operations domain.
By Muhammad Bin Khamis Butt (Bilal Mustafa & Muddassar Yaqub Rathore) – Engro Fertilizers Limited, Daharki, Pakistan
Dynamic & respected leader effectively managing and empowering his team to achieve organizational goals. Combine excellent communication & interpersonal skills with unquestioned ethics and a dynamic hands-on approach.
Experieced professional (7 yrs), with practical HSE system implementation experience at a Petrochemical Complex (downstream oil & gas). Conversant in budget preparation and monitoring of Fixed & Variable Costs (OPEx & IP). Adequate experience of Six Sigma, 5S & Auditing.
Connect with him on LinkedIn